IMR HAMBURG SKILL TRANSFER
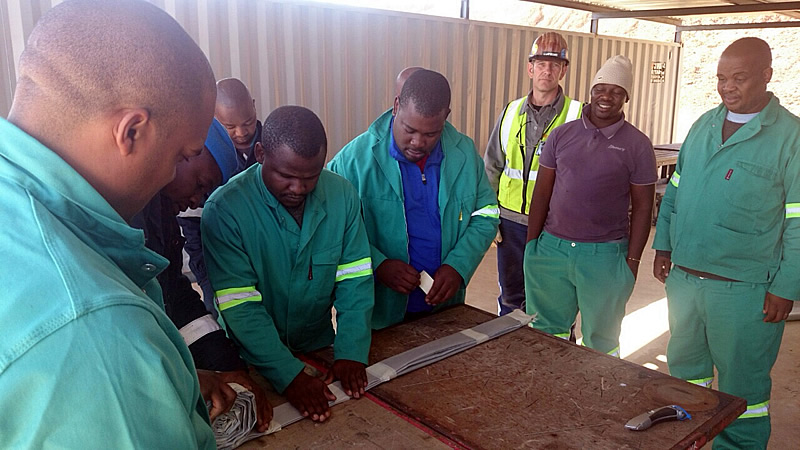
June 2014: IMR Hamburg is executing during the erection of high pressure pipelines in the Kusile Power Station successful the Skill Transfer to the local workforce from Witbank South Africa. The local employment on the project through IMR is drastically increasing. An education on the job is happening through the Know How transfer from Europe […]
IMR Hamburg AFRICA to celebrate an anniversary of the 1st annual year of business acomplishment in South Africa
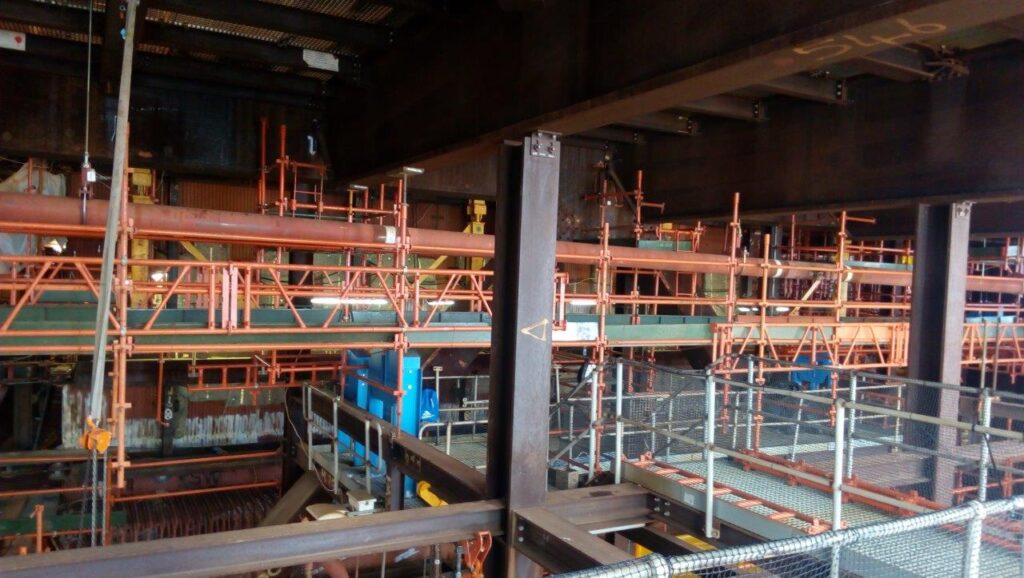
Due to the 1st Anniversary of Business dealing on the South Africa territory, the employees of our Company have organised the weekend trip on the Johannesburg area. The trip organiser that means the celebration of our 1st. Anniversary of Business dealing Mr.Andre Koehsel, the head manager of branch office of the Company in the South-Africa, […]
IMR Hamburg extends business in South Africa on Kusile project
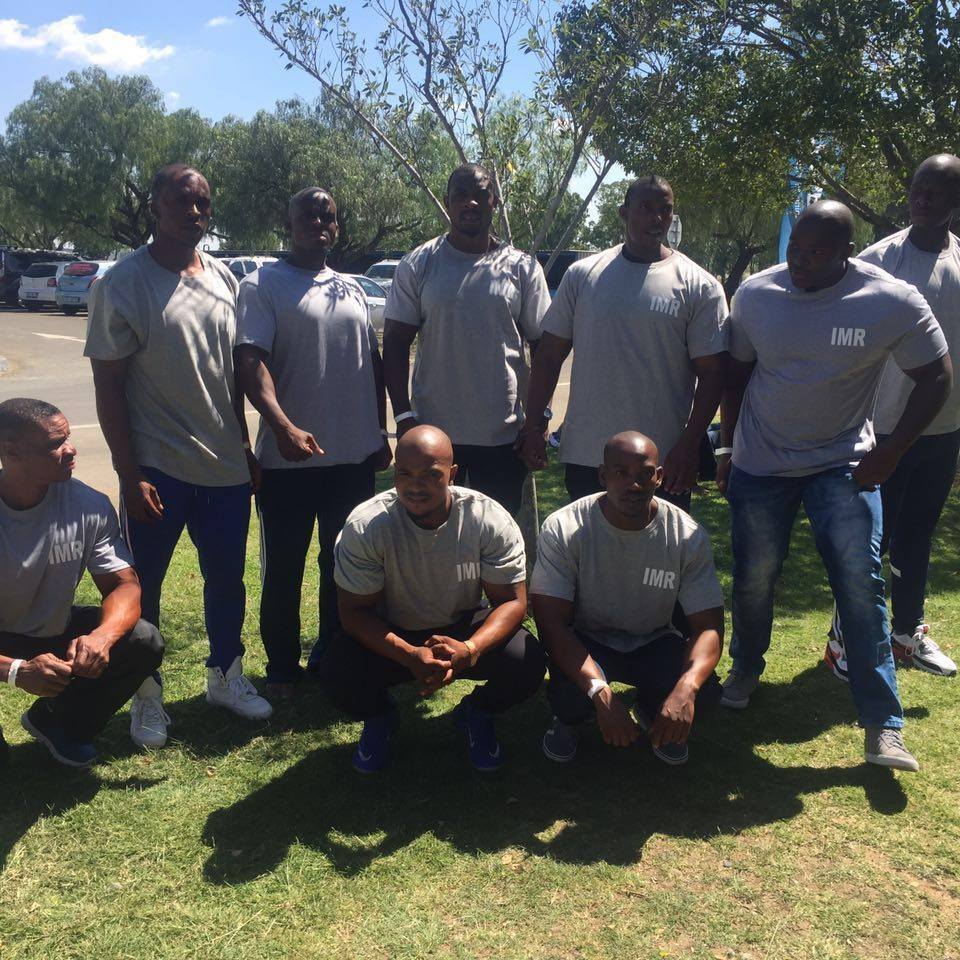
The company IMR Hamburg has successfully extended the project contracts for the installation of low pressure and high pressure piping on Kusile with the contractors who are responsible for installation of the turbine and boiler house at 6 x 800MW thermal power plants which is built by the state owned energy supplier. On the IMR […]
Revision RWE KW Neurath Block G
Im Mai 2013 hat die IMR an der Revision teilgenommen. In diesem Zeitraum wurden einige Russbläser sowie zugehörige Rohrleitungen angepaßt und ergänzt. Die Fehlerquote von ca. einhundert geröngten Schweißnähten betrug 0%. Aufgrund der guten Leistung wurde die IMR auch für die Revision von Block F für August 2013 bestellt.
New prefabrication area in Bakum-Harme near Vechta
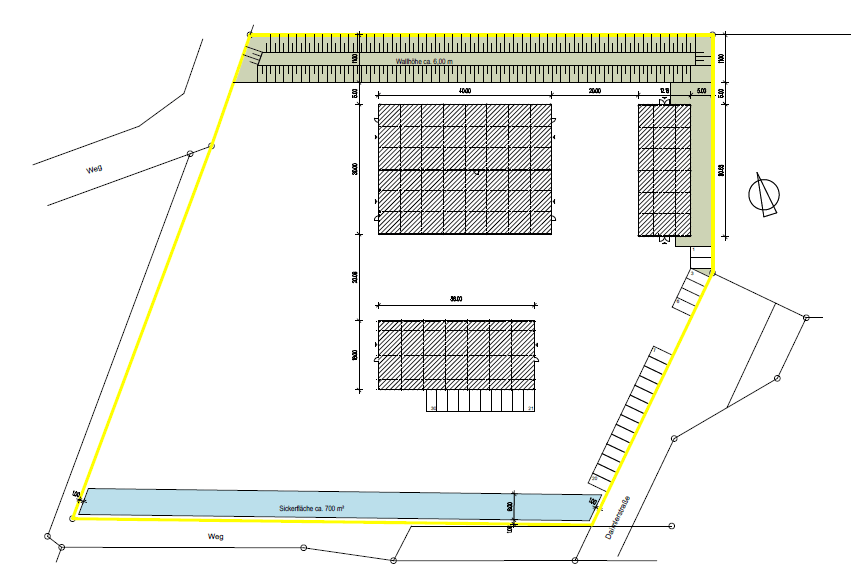
Our new prefabrication area conveniently situated just next to the motorway (Autobahn) A1 will be constructed in Autumn/Winter 2009. Prefabrication of spools for the new construction sites in Northern Germany will take place there.
Auditing of Procedures “P92” successfully completed
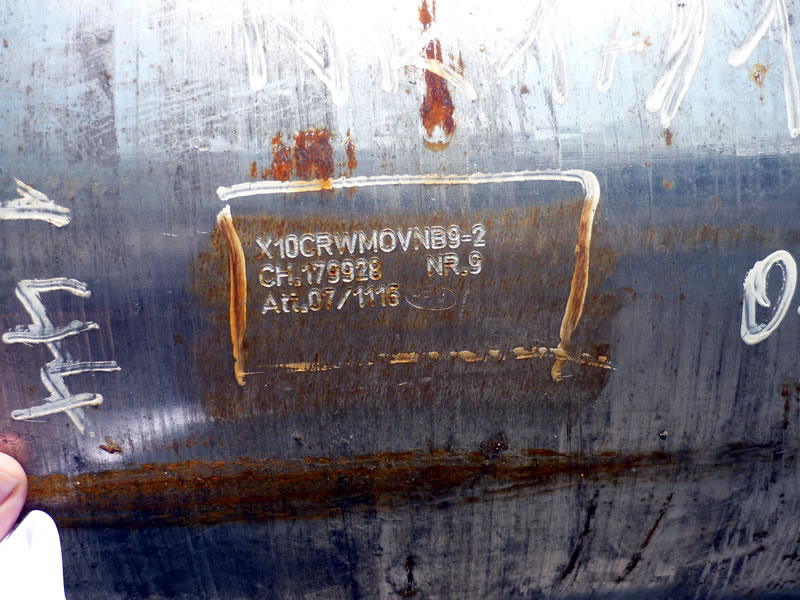
In May 2009 auditing of procedures Rohr 33,7×8.0mm and 396*30mm for the material X 10 CrWMoV 9-2 material- Nr. 1.4901 were tested through weld verification as well as NDT (company Pockrandt www.pockrandt-tqs.de) and through destructive testing (Germanischer Llyod Prüflabor, Herne). In cooperation with the TÜV Nord (Western area, Essen region, www.tuev-nord.de) the Vallourec&Mannesmann basic material […]
SmartPlant Isometrics and PiCoDa launched
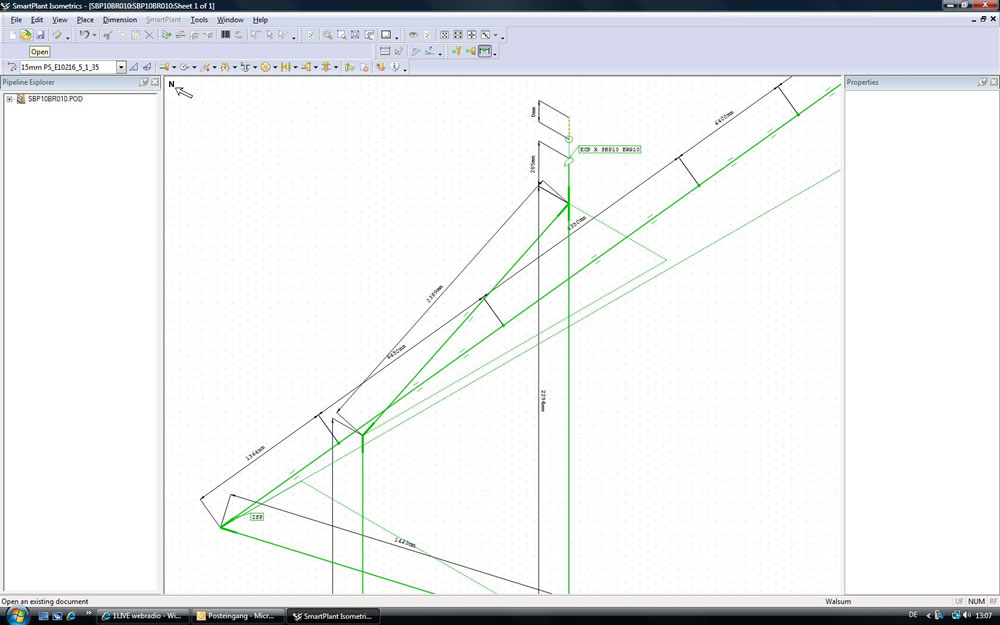
October 2009: In Cooperation with Hitachi Power Europe GmbH IMR has successfully introduced different Software-Solutions from the Piping Solution of Intergraph PP&M Germany GmbH. With the help of SmartPlant Isometrics based on the ISOGEN-Standard 80 KKS within small bore piping have allready been designed. The KKS respectively the Isometrics and the associated bill of material […]
IP LP piping package Wilhelmshaven ordered
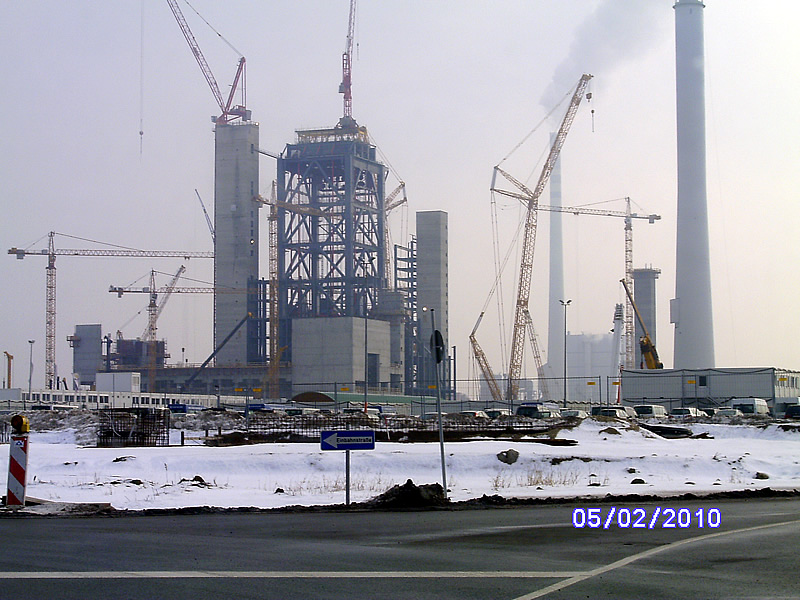
WHV EBL Ansicht In December, 2009 the order was given to IMR for manufacturing and erection of IP, LP and partial HP piping systems of the project „New building of KW Wilhelmshaven Electrabel W1“. The customer Hitachi Power Europe GmbH (HPE) from Duisburg builds there essential components of the new 800 MW coal power plant […]
Safety at work initiative 2011
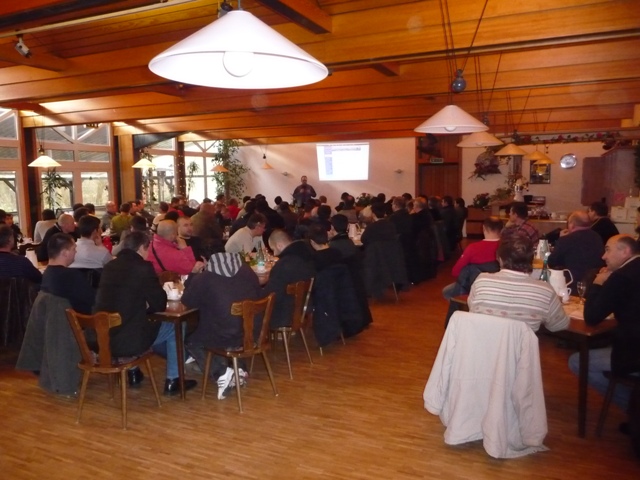
In CW06-2011 the entire personal employed in the new building on CFPP Wilhelmshaven by IMR operational personal and executive staff where trained and tested in accordance with SCC Doc. 18 and 17. As a campaign for safe, healthy and environmentally sound work aims IMR in continuous improvement under this years motto of our BG (work […]
P92 WPQ with wall thickness range over 120mm
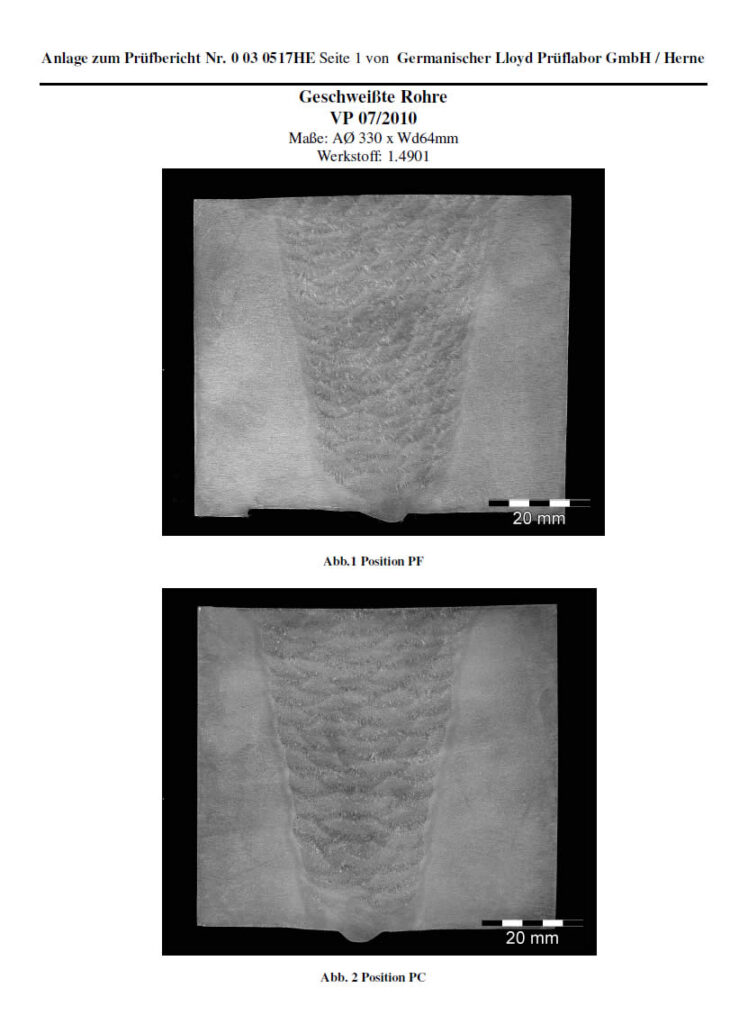
In the competition as a system supplier for assembly and welding technology of e.g. fresh steam pipes and turbine connections strives the IMR further at the head in the processing of the material X 10 CrWMoV 9-2 (material number 1.4901). The long winter was used to weld together in January 2010 pipes from the so-called […]